Industrial building
Heckington Windmill
Heckington Windmill is the only eight-sailed tower windmill still standing in the United Kingdom with its sails intact. This Grade I listed windmill was built in 1830 with five sails. Damaged in a storm in 1890, the mill was repaired using eight sails, the cap and machinery from a local windmill in Boston. The mill has six storeys called "floors": ground floor, meal floor, stone (stage) floor, lower bin floor, upper bin floor (hoist floor), dust or cap floor.
Skills used at Heckington Windmill
The Traditional Millwright
The traditional millwright was the forerunner of today’s mechanical engineer with multi-disciplines. He also had to combine civil engineering skills such as assessing the levels and flow rates for water supply to power waterwheels and turbines.
He had skills in carpentry with intimate knowledge of the strengths and properties of the wood he used for different components.
- Traditionally, oak was used for timber framed buildings, including the main components of post and smock windmills.
- Imported Baltic softwood was used increasingly in Lincolnshire and Yorkshire for making sail frames, flooring beams and boarding during the 18th and 19th centuries.
- Elm was a favourite for gear wheel rims that carried wooden cogs, which were usually shaped from Hornbeam, Apple and other fruit woods.
The millwright would be capable of working out gear ratios and making and assembling gear wheels and shafting. Increasingly during the 19th century cast iron was used for these components with finer pitch for the teeth.
Routine maintenance including stone dressing, repairs and replacing of machinery components and external painting of mills were also a mainstay of their income.
The graft of the modern millwright is greatly reduced by the use of power tools and modern heavy lifting gear together with access to sawmills and foundries etc. There is no formal training or qualifications in becoming a millwright. New millwrights generally learn through informal apprenticeships working for existing millwrights. There have been moves in recent years to set up a national training scheme and it is hoped that they will bear fruit in the future. There is an urgent need to train young artisans in traditional millwrighting skills by those with the required qualifications.
Windmill sails
Until the later 18th century hand clothed sails were universal on English mills, giving rise to their alternative name of Common sails. The sail frame had a canvas sheet spread over the lattice framework to catch the wind, on the same principle as setting sails on a sailing ship, the cloth would be reefed according to the wind speed or power required.
From the late 18th century onwards, much thought was put towards developing semiautomatic sailcloth adjustment, initially using a set of rolls of canvas or individual shutters connected like a Venetian blind to allow them to open and close in unison under the control of an adjustable spring arrangement. Various other patents were registered, but the most popular was William Cubitt’s, patented in 1807, and the most common type to be found in England today.
Sail construction, like vernacular architecture, varied according to local custom with different angles of weather to suit the types of wind prevalent in different areas. It is important to recognise these regional variations and try to replicate their salient features to preserve traditional patterns.
The traditional way of erecting the sails to the front, or Poll End of the sail axle, Windshaft, was to mount the sail frames, to a longer and stouter piece of timber, called a stock which passes through and is wedged into the end of the windshaft or through a cast iron box or poll end. A sail was secured to opposite ends of the stock, two further sails were then fitted on another stock at right angles to the first.
In Lincolnshire, Yorkshire and some East Midland counties, stocks were dispensed with, and individual sails with stouter whips, called sail backs were secured to the arms of a cast iron cross to give a much stronger mounting. Crosses were made with four, five, six and even eight arms to allow more power to be developed.
All of these types were once to be seen in Lincolnshire, which at one time boasted more multi-sailed windmills than any other county. Heckington’s impressive mill is the last of its type to carry eight sails in the UK.
Industrial brickwork
Solid brickwork or masonry was the norm until the early 20th century when cavity wall construction was developed. Various brick bonds were used, English bond, having alternative courses of headers and stretches was the oldest and was still used well into the 19th century where strength of brickwork was a consideration including bridge building, waterwheel chambers and lower courses of industrial buildings including tower mills built on unstable subsoils, (Sanderson, the Louth millwright specified the use of English bond on most of the new tower mills he fitted out up to the late 1870s).The usual bonding found in later 18th century and 19th century industrial buildings was a variation of the English Garden Wall bond with three or more courses of stretches between a course of headers.
Professional bricklayers would normally be employed to construct building millwright would work with them to fit the machinery as the building progressed. Round windmill towers and chimneys required special consideration in construction, a trammel from a centre point and a batter plumb were used to maintain the circle and batter of the tower. Lime mortar was employed in the building trade until the harder Portland cement was developed by the 20th century. When building a brick tower mill, the strength of the lime mortar mix would be weakened as the tower reached its upper limit to allow more elasticity and reduce cracking caused by the weight and movement of a rotating cap and sails. Offsetting of windows to successive storeys was also considered good practice to prevent severe cracks down the tower. Care was also shown in providing sufficient fall on the windowsills to allow rainwater run-off.
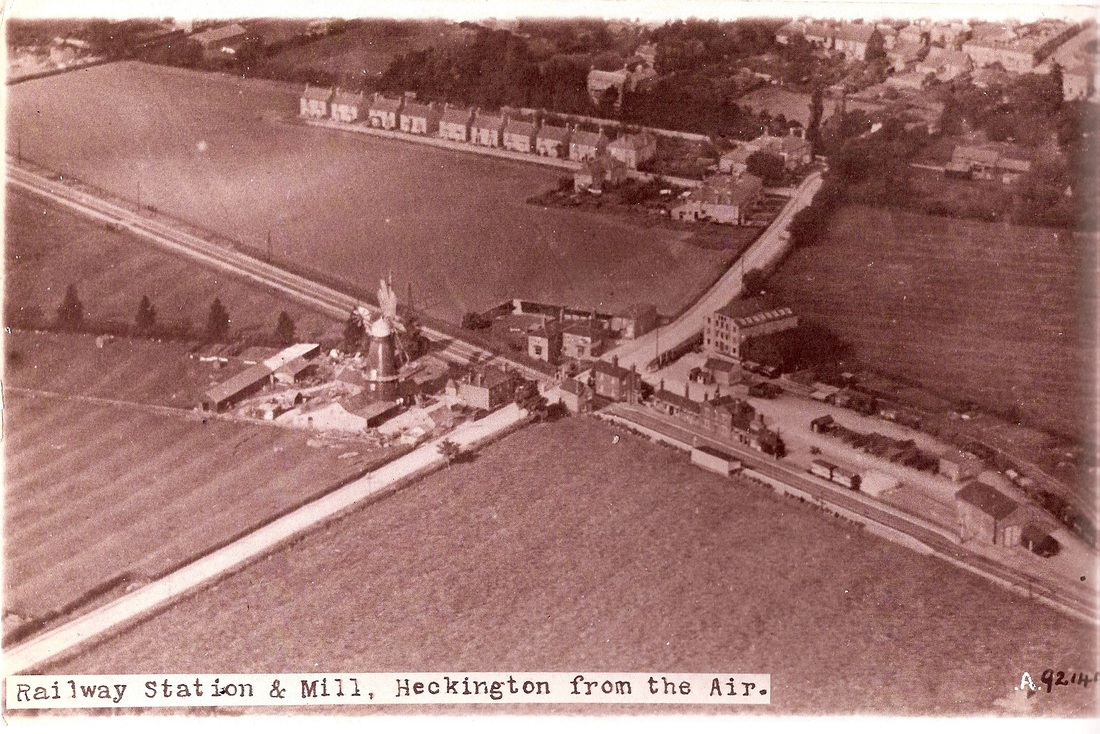
In the days when new mill towers were being built, the quality of early bricks varied depending on local clay quality and kilning technology. The need to apply an exterior weatherproofing coating of a lime wash membrane or later gas tar derivatives usually denotes a softer, porous brick being used.